Novel approaches to home building
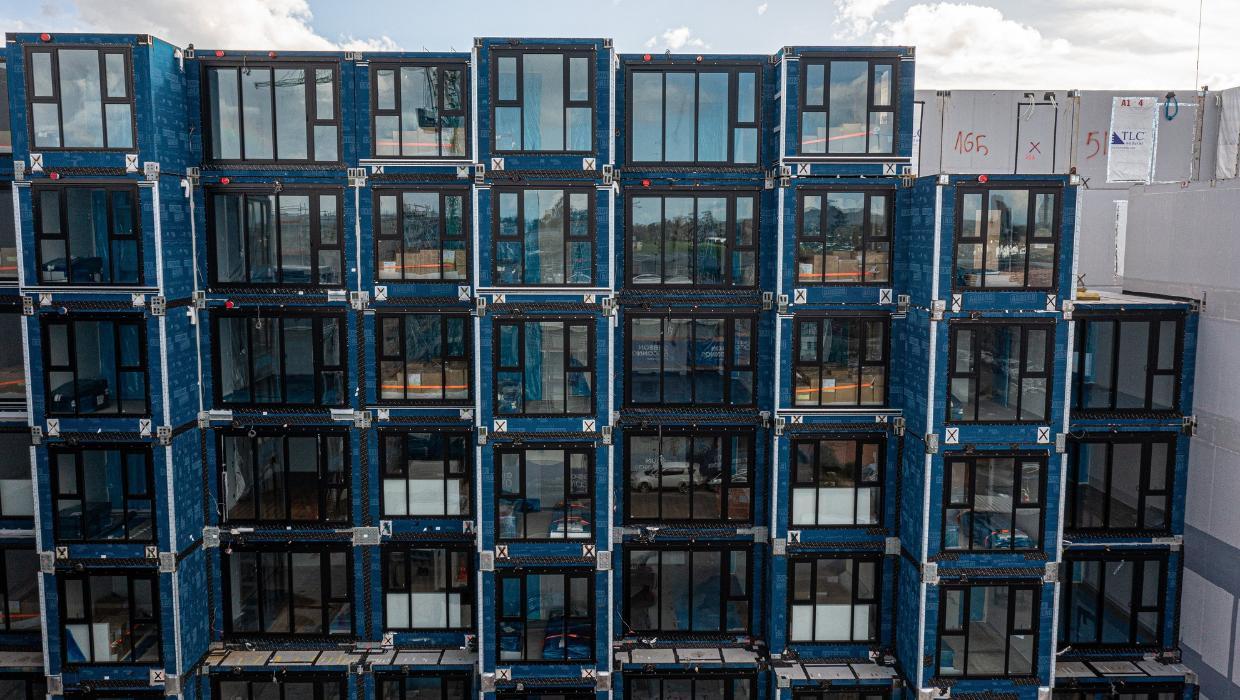
Thinking outside the conventional building box
Australia’s housing market has seen rapid price inflation and worsening affordability. House prices surged by 26% since 2019 and have nearly doubled since 2009. While affordability metrics, such as the income-to-house-price ratio, have reached unsustainable levels in many cities. For instance, in metropolitan areas like Sydney, the income-to-house-price ratio has reached as high as 10.8. This leaves many Australians priced out of both homeownership and rental accommodation.1 In response, policymakers have set ambitious targets, aiming to deliver 1.2 million new homes over the next decade. However, current construction rates suggest there is likely to be a shortfall of approximately 300,000 homes at the end of the decade.2
Conventional methods to increase housing supply remain essential. But they have been unable to keep pace with the task at hand. Could Australia explore more innovative, novel construction approaches? Ones which would deliver homes more quickly and at a lower cost?
Non-conventional methods have been implemented in other countries throughout the world. These include New Zealand, the United States, Canada and the United Kingdom. In this article, we explore four novel approaches to building houses. Approaches that could potentially offer a solution to Australia’s housing crisis.
Modular Housing
Modular housing was first introduced in the 19th century. But modern modular construction gained traction in the 1930s. Significantly evolving with technological advancements over time making it more efficient and effective.3 Modular housing involves constructing large sections of a building off-site in a controlled factory setting. These modules are then shipped and assembled on location.
Studies show that this method can reduce construction time by up to nine months. Enabling occupancy within three months. It also lowers building costs by around 30% compared to traditional on-site construction methods.4
A leading project in Auckland, New Zealand successfully delivered 76 modular homes within record times. This approach reduced construction time by 40% and resulted in a cost saving of around 30%. Resulting in a completion time of about 7-8 months. Whereas, a conventional apartment development would have taken around 1.5–2 years to complete. A modular approach also provided a consistent quality standard and reduced on-site waste. The build cost came in around $4,200/sqm, compared to $6,000/sqm for conventional low-to mid-rise apartments.5
Similarly, Vancouver, Canada has integrated modular housing into affordable housing projects. This was an attempt to combat the city's homelessness issue. A total of 600 modular housing units built in around three months to accommodate the homeless population.6
The global modular home market is valued at US$103.6 billion in 2024. Its expected to increase to US$163.5 billion by 2043. This equates to an average growth rate of 7.9% per annum.7 This demonstrates a strong demand based on its time efficiency and cost savings. This could offer a scalable solution to Australia’s growing housing shortfall.
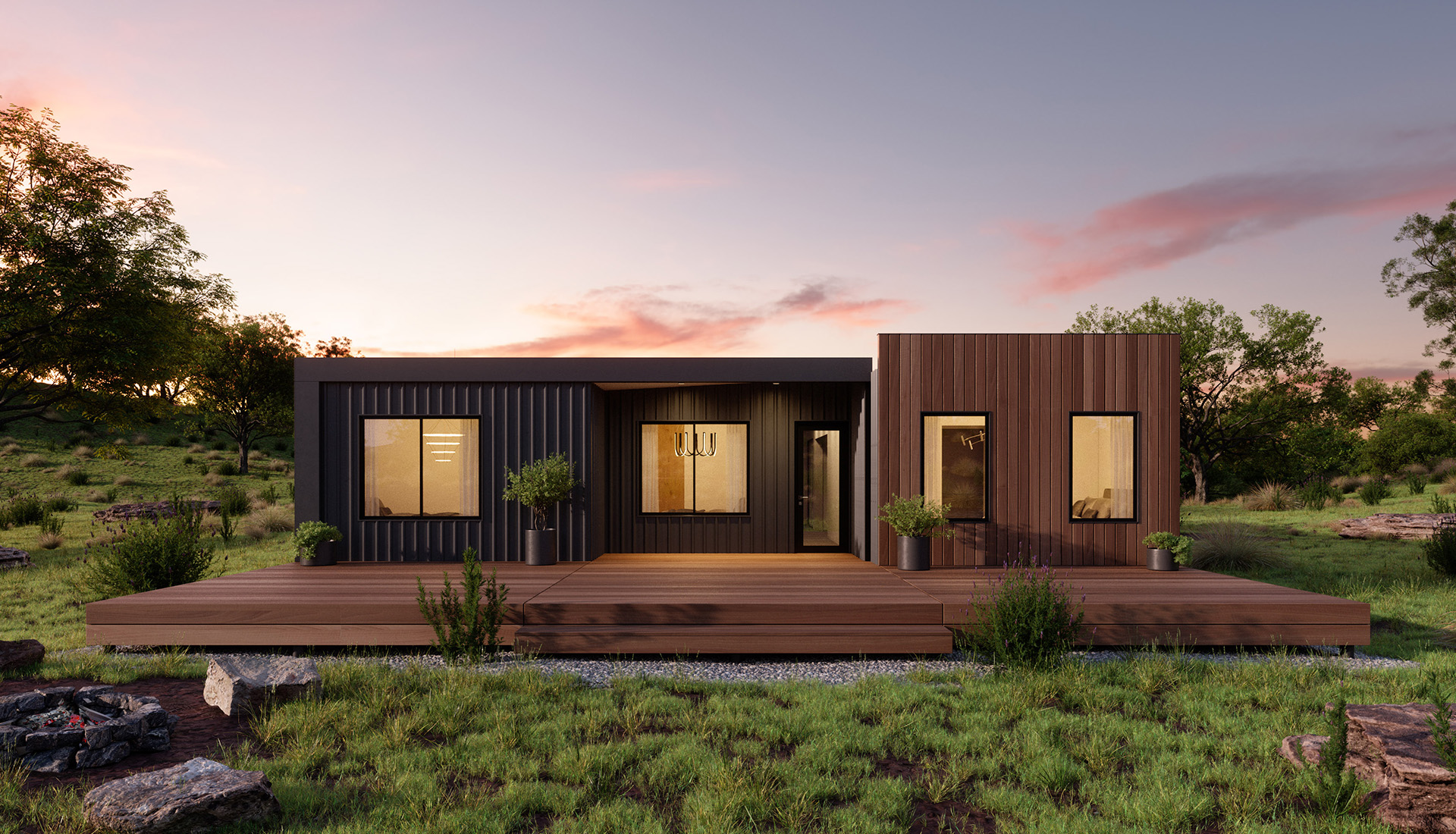
3D-Printed Houses
The concept of 3D-printed homes emerged in the early 2010s. The first full-scale 3D-printed house was completed in 2017. 3D-printing in construction employs large-scale printers. These deposit layers of concrete or composite materials to form walls and foundation structures. All done with minimal manual labour.
Early 3D-printing projects have demonstrated up to a 25% reduction in costs. As well as a 50% reduction in build times compared to conventional methods. For instance, a pilot project for a three-bedroom house in Riverhead, New York took a total of 80 hours to 'print'. The process carried out over the course of a few weeks. Upon completion, it was then listed for $299,000. This is a significantly lower price than the area's median price of $450,000. This equates to a 3D-printed house costing 50% less to build. Approximately $151,000 less in costs.8,9
In Los Angeles, an entire neighbourhood consists of 100 plus 3D-printed homes. The project delivered fully functional dwellings with construction costs reduced by approximately 30%. It also cut labour costs by 60% compared to traditional methods. Demonstrating the technology’s potential to address labour shortages and speed up housing delivery.4,8,9
Although still an emerging technology, the 3D-printed housing sector is rapidly growing. In 2023, the global market for 3D-printed homes estimated to be around US$0.89 billion. But it is expected to grow to US$1.63 billion in 2025 and to around US$24.50 billion by 2034. Achieving an average annual growth rate of around 35.1% per annum.10 As the technology matures and cost barriers reduce, 3D printing will capture a niche market. With the potential of expanding its reach and interest to wider markets.
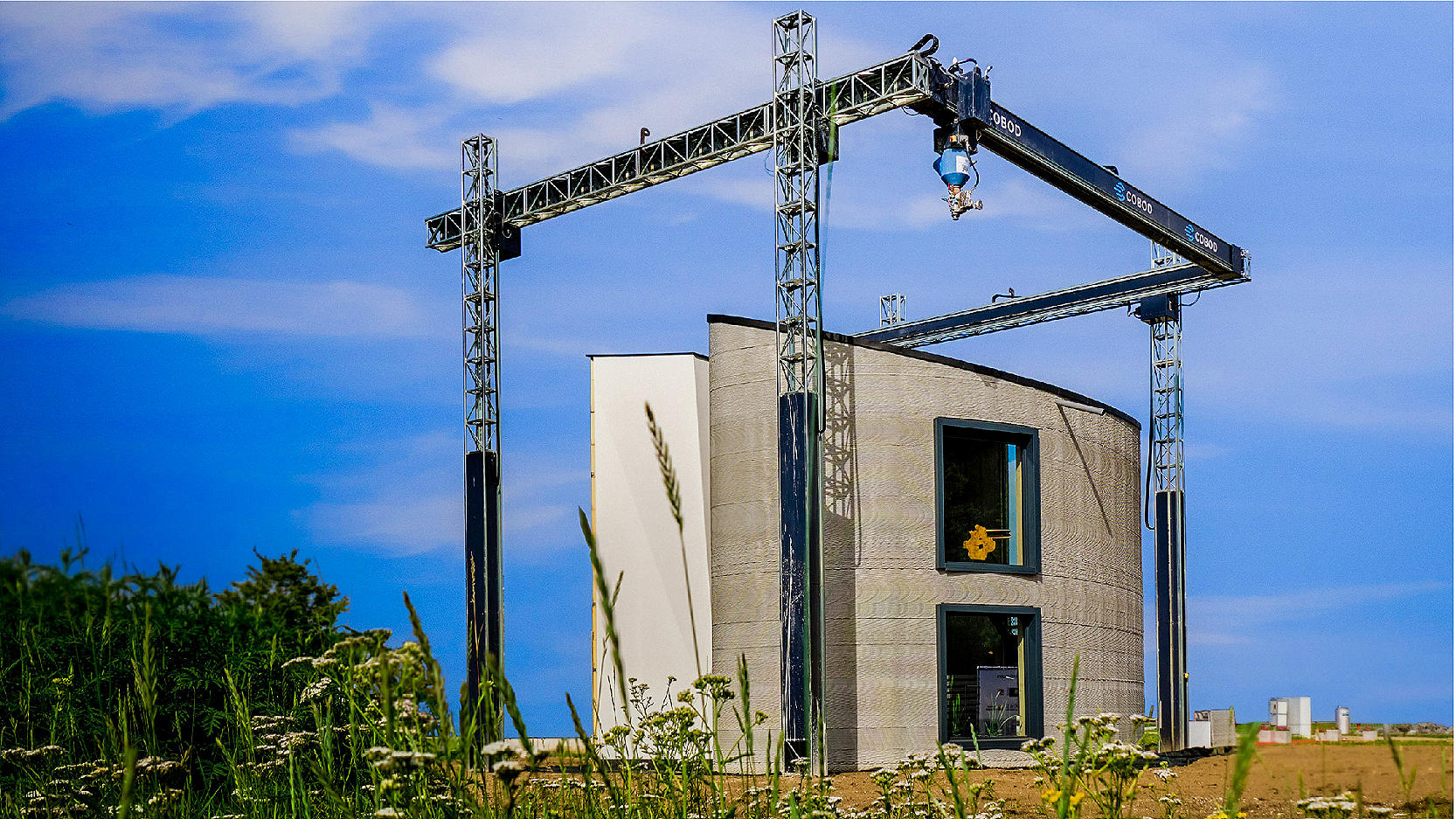
Shipping Container Homes
The idea of repurposing shipping containers for housing emerged in the 1980s but has gained wider adoption in the last two decades. 11. Shipping container homes repurpose decommissioned shipping containers into habitable living spaces.12
In Vancouver, a groundbreaking project transformed 12 shipping containers into affordable housing units. The initiative delivered significant cost savings, reportedly cutting costs by approximately 50%-60%. The total cost of repurposing the shipping containers was CA$82,500 compared to CA$199,000 for a 27sqm area.12
In Auckland, an apartment development consisting of 183 units also showcases the viable use of shipping containers. Within a few months, a six-storey building was assembled 'like Lego’. The first 79 apartments were ready for occupants to move in within 7-8 months. The average price of a typical New Zealand apartment sits around NZ$1.25 million. These container homes were priced at an average of NZ$750,000, dropping approx. NZ$500,000 off the price often seen for conventional homes.13,14,15
In 2023, the market size valuation for container homes was US$61.8 billion. It's expected to grow to US$108.7 billion by 2032, achieving an average growth rate of around 6.7% per annum.16
The cost-effectiveness and sustainability of container homes make them an attractive option. Especially for urban infill projects and for rapid-response housing in crisis.
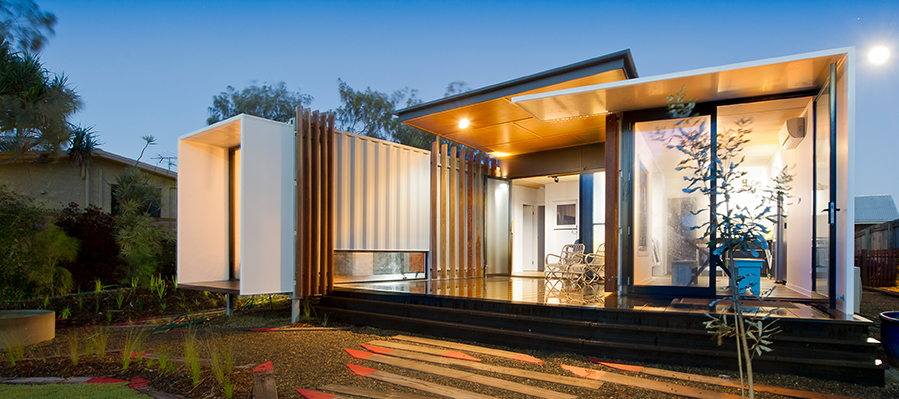
Micro-Apartments
Micro-apartments are compact and highly efficient living spaces. They are designed for dense urban environments and range from 25sqm to 35sqm. Micro-apartments are typically 20%-30% cheaper to buy than conventional housing. Making home ownership more attainable for many more people. In central London, a micro-apartment development achieved a remarkable 95% occupancy rate within the first six months of launch.17
The success of micro-apartments in London illustrates their potential to transform urban housing markets. With rising property prices and shrinking living spaces, micro-apartments could be well-positioned to capture significant market share in major cities worldwide.
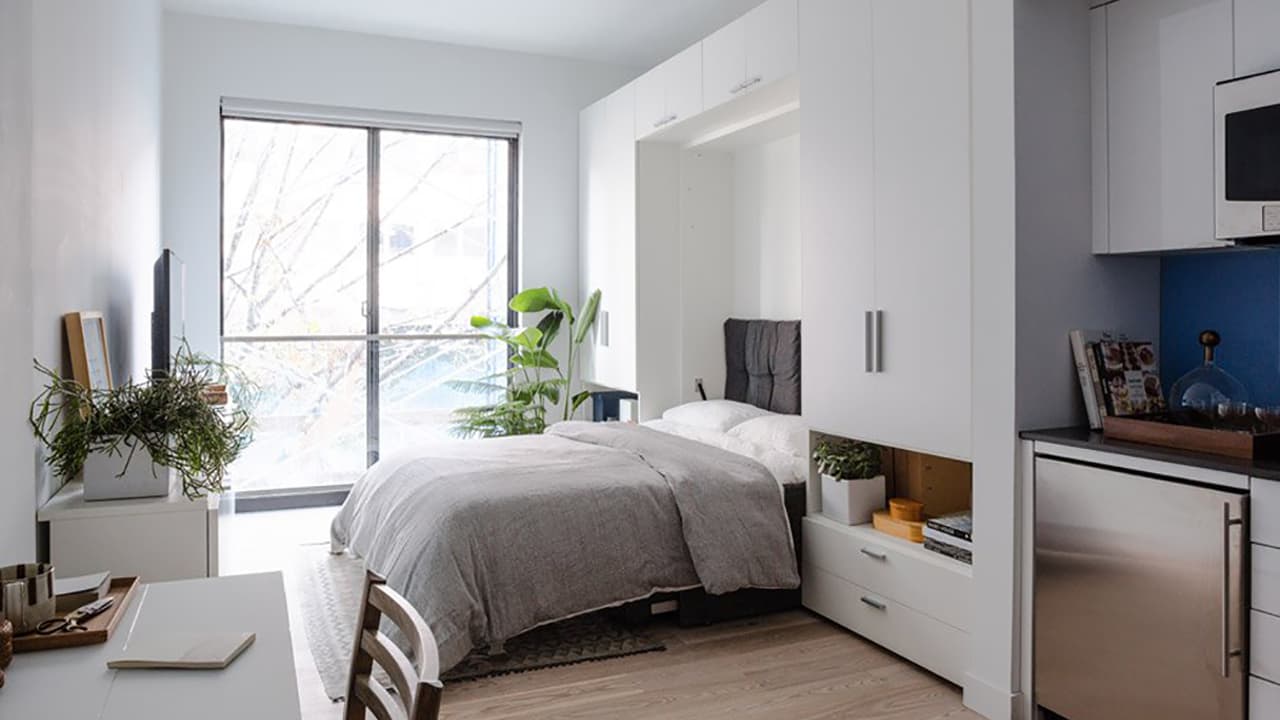
Thinking (and implementation) outside the conventional box needed
Australia’s housing crisis is a complex challenge that demands non-conventional, innovative solutions. While traditional construction methods have their place, they are not enabling rapid response and an affordable cost.
Novel approaches to building homes offer transformative potential. Could Australia leverage some of these novel construction approaches? Ones that deliver faster, more cost-efficient and sustainable housing solutions? And are proving to be successful overseas?

References
- ANZ/CoreLogic Housing Affordability Report. (2023). Housing Market Analysis.
- https://www.realestate.com.au/news/australia-home-building-targets-why-the-nation-is-not-close-to-meeting-its-ambitious-12-million-homes-goal/
- Piqueras Blasco, M., & Cabrera i Fausto, I. (2024). Prefabricated Housing Construction Throughout History. archiDOCT, 12(2), 33–41.
- McKinsey & Company. (2023). Modular Construction: From Projects to Products.
- Modular Housing Case Study in Auckland (2024); https://www.dracon.co.nz/single-post/a-new-zealand-modular-housing-case-study-the-future-of-mass-housing-made-in-china
- SQ4D 3D Print Housing Pilot. (2022). Pilot Project Report – Austin, Texas.
- ICON. (2023). 3D-Printed Housing: The Future of Affordable Construction.
- Blanford, M., & Bender, S. (2020). Upcycling shipping containers for houses. Cityscape: A Journal of Policy Development and Research, 22(2). U.S. Department of Housing and Urban Development, Office of Policy Development and Research.
- https://www.fortunebusinessinsights.com/container-homes-market-107142
- https://www.pocketliving.com/?form=MG0AV3
Related posts
Dive deeper into insights that matter to you.
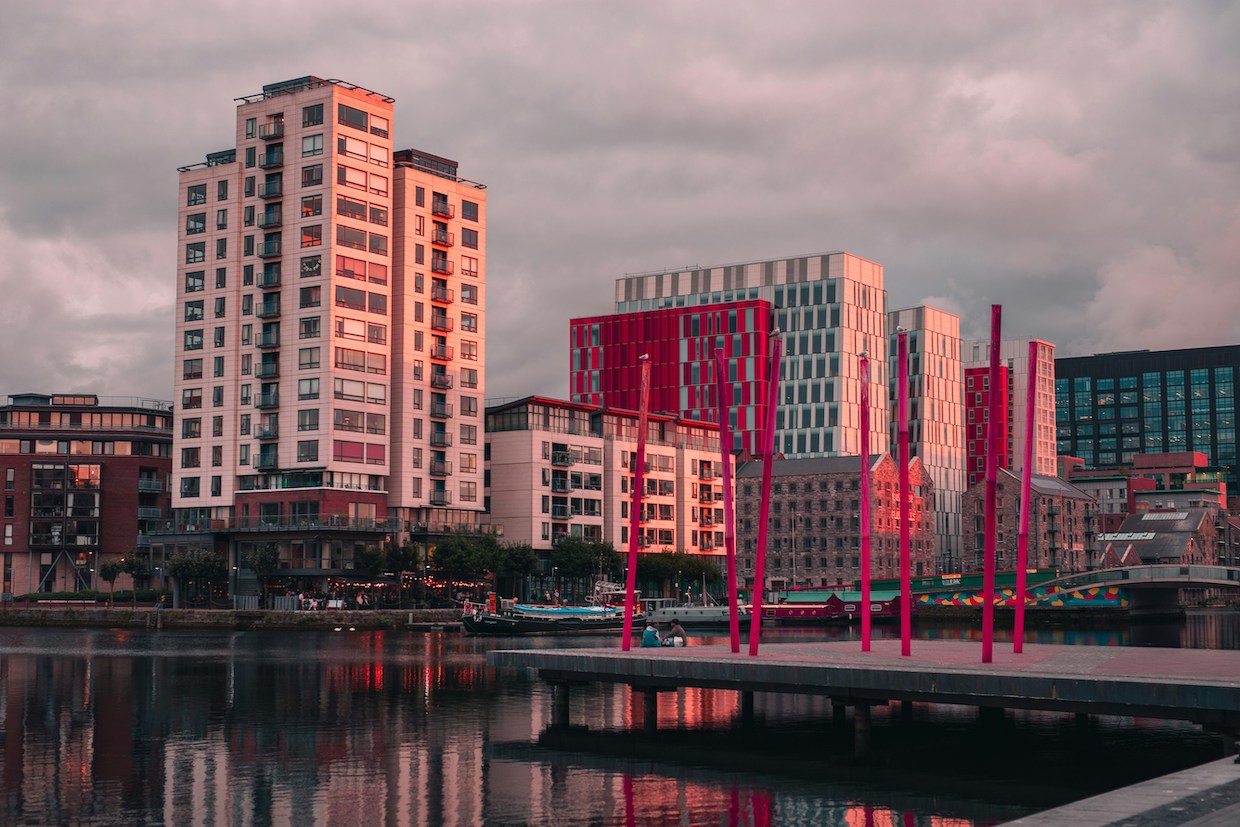
The Election and Housing: Ireland’s Wake-Up Call for Oz
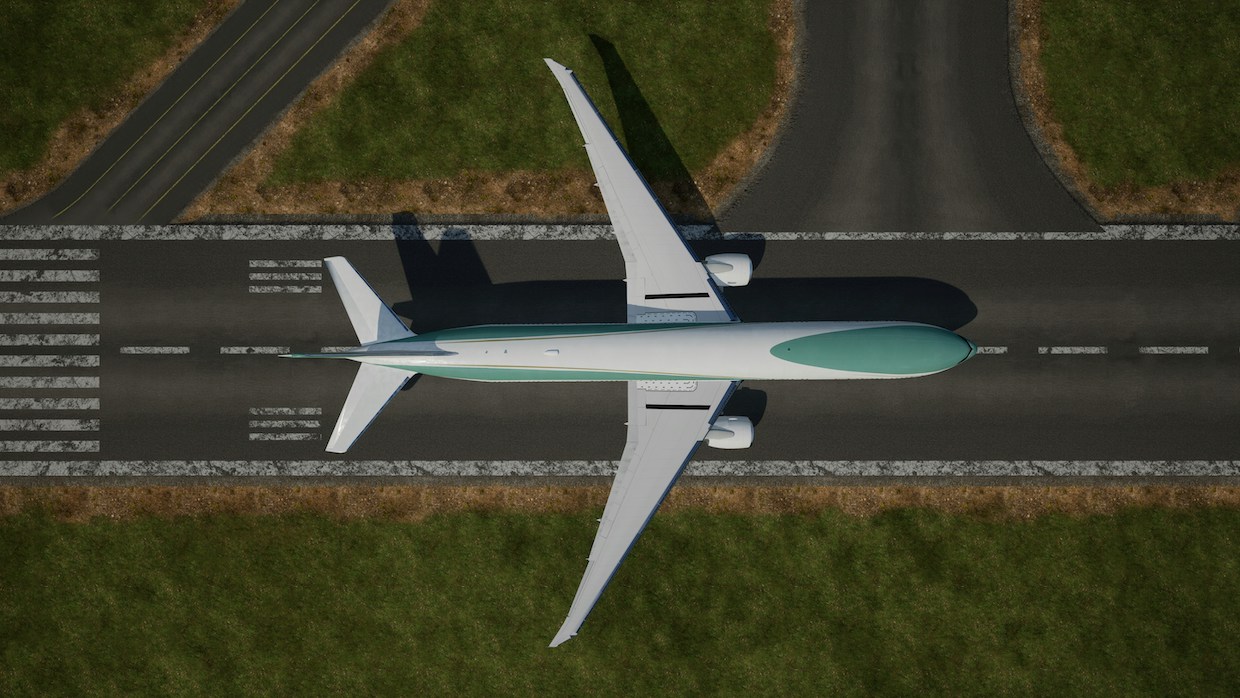
Australia’s Visitor Economy Rebounds: Insights from 2024-2025 ABS Data
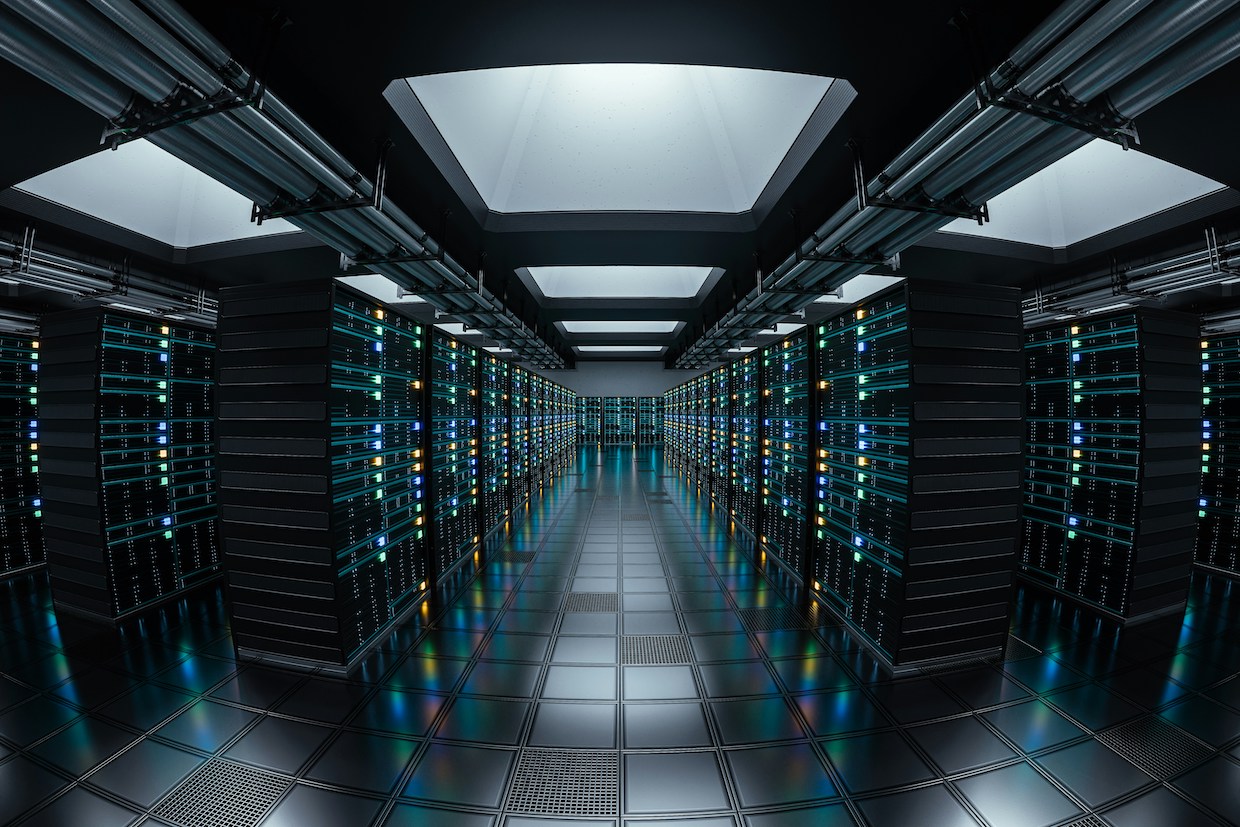
Australian Data Centres: The State of Play for this Critical Sector
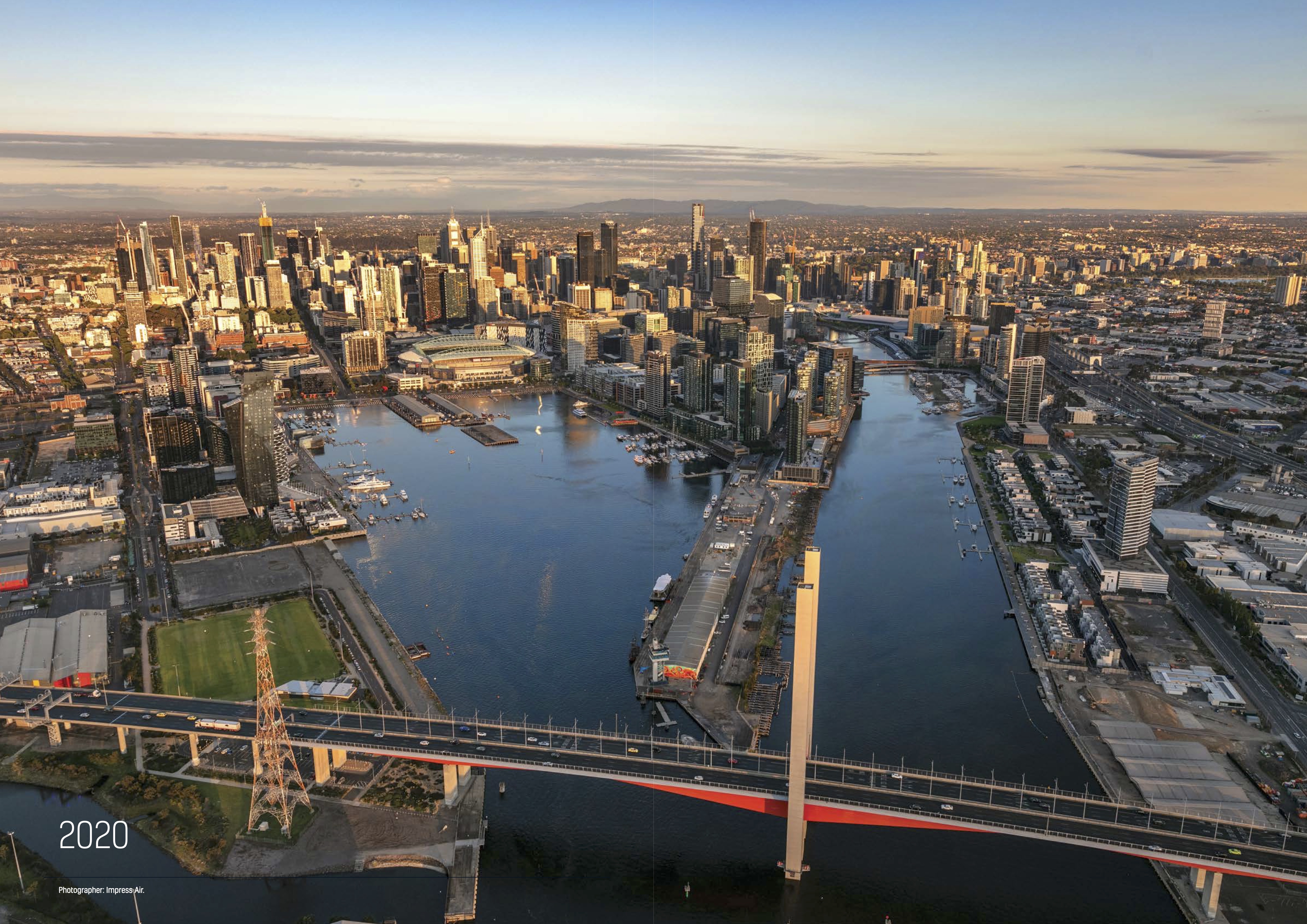
30 Years On: Has Docklands Been A Success?
Make smarter decisions
Get in touch with the Team to get an understanding of how we transform data into insightful decisions. Learn more about how Atlas Economics can help you make the right decisions and create impact using our expertise.